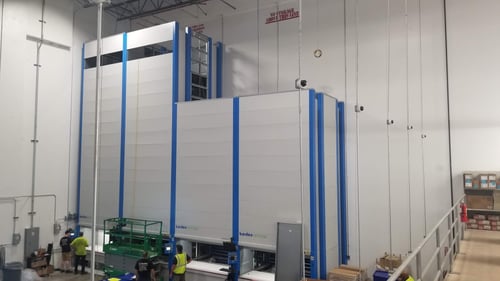
Buying ASRS, new or used follow this guide
You’ve decided to take the plunge on an automated storage and retrieval system (ASRS) – great! They offer many advantages for warehouse inventory management and order fulfillment centers, manufacturers, equipment and automotive companies, logistics firms, and any organization that requires storage and quick access to records, supplies, parts, and tools.
Your budget is always a top concern, so a used system can be quite appealing. But before you purchase a used system, be sure you’re considering the full picture. Keep reading to see the questions to ask yourself before you buy.
1. How Often Will it be Used?
Depending on what you’re storing, you might use the system a few times a week or multiple times per shift at all hours of the day or night. A used system with high “mileage” may not be able to keep up with your usage patterns.
2. What Condition is the Unit in?
Learn as much as possible about past wear and tear, what it held, the facility environment, and maintenance records. Consider getting an independent inspection of the unit to ensure it’s in the shape the seller claims it to be. This is especially important if this is your first experience with ASRS equipment.
3. Is the Original Documentation Included?
Sometimes you need to read the manual to understand how to get the equipment up and running and integrated with your other systems. Documentation also makes it easier to troubleshoot problems, adjust the configuration (if possible), or contact the manufacturer. And when you have a workforce to train on the new equipment, documentation provides the extra details you might not pick up intuitively.
4. Is the Unit Exactly What you Need?
Consider how much flexibility the unit has regarding the configuration of shelves and dividers, bins for small items, shelf height, weight limits, and more. If organizational components like tubs and bins aren’t included, can you buy them separately?
5. Does it have Up-to-date Safety and Ergonomic Features?
Sensors and programmable controls that detect movement or avoid collisions are improving all the time to keep workers safe. Likewise, equipment that can be configured to minimize bending, reaching, pulling, or lifting reduces injuries and fatigue.
6. Is Service and Support Included from the Seller of a Used Unit?
One advantage to buying a new ASRS is access to ongoing support and service from factory-certified technicians. Moving is hard on equipment, and once it’s been disassembled, reassembly can be a challenge. A related challenge is if something breaks or is damaged during disassembly, moving, and installation. Replacement parts or repairs may not be available for used equipment.
7. Is a Warranty Included?
Warranties are rarely transferrable and not always offered with used equipment. Be sure to review exactly what is covered, what is not covered, and how long any warranty lasts on used ASRS units.
8. Does it Fit Your Existing Set-Up?
This refers to integrating with your ERP, warehouse inventory management software, order picking system, and other automated equipment you have in place, such as conveyors or robotic packaging systems. It also includes how well it fits into your space (not only in its final location but on your loading dock, moving through the doors, down any corridors, etc.). Consider how to plan for the logistics and any additional expenses incurred.
9. Can the System Evolve with Your Business?
As you look toward later business development, think about the available options for retrofitting or upgrades should you require more, less, or different storage space. If you foresee moving facilities in the future, a new equipment vendor like Kardex offers relocation services as your needs change over time, including:
- A customized moving plan created by our in-house professionals.
- Factory-certified and experienced technicians.
- Disassembly without causing damage (in some cases, units can be moved intact).
- Efficient transportation to the new location.
- Quick and accurate reinstallation.
10. Are you Looking at the Big Picture When it Comes to ROI?
Any ASRS unit is a big investment. But when determining how long it takes to recoup that initial outlay, be sure you’re looking at all the savings and opportunities that come into play. Some examples of the benefits of automated storage and retrieval systems contribute indirectly but significantly to your bottom line and offset the price, such as:
- Reclaiming floor space can be used for growth opportunities (such as more workstations or adding a kitting station or automated packaging line).
- Increased productivity due to reduced travel time on order picking.
- Avoiding errors (and the time it takes to correct them) with light-guided or other picking technology.
- Processing the same or larger amount of orders with less staff.
- Less time spent looking for and retrieving tools instead of getting work done.
Finally, remember that a new customized unit doesn’t have to mean the top-of-the-line, fanciest model. Rather, it should include the specific features and capabilities you need and nothing you don’t (for instance, appropriate size, storage density, and weight capacity).
ASRS can achieve major gains in productivity by reducing travel time in order picking, faster retrieval and storage of tools, and expanding operations by reclaiming floor space. But if the unit isn’t set up for your unique needs, it may actually hinder the advantages.
There is so much to think about when investing in ASRS equipment – please contact Kardex to discuss the types of automated storage and retrieval systems, your requirements, and your options!